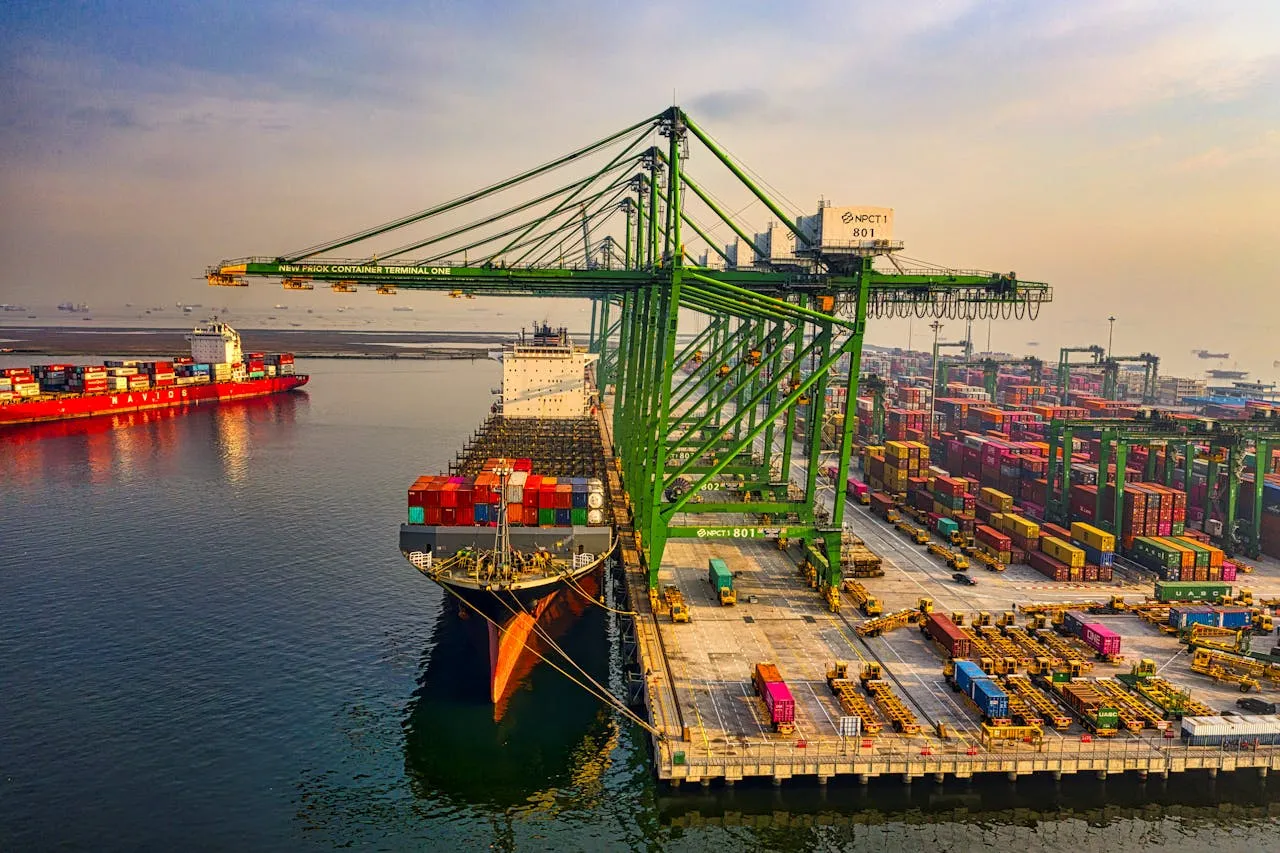
Kao USA Boosts Logistics with SAP Upgrade and Warehouse Merger
Efficient logistics operations are crucial to the success of any business, but they take on heightened importance within the fast-moving consumer goods (FMCG) industry. The inherently short product life cycles, rapid turnover, and high consumer demand place immense pressure on companies to optimize every link in the supply chain. For Kao Corporation, a Japan-based global leader in the manufacture of personal care products, household items, cosmetics, and specialty chemicals, streamlining logistics operations across its Americas region became a strategic imperative.
In recent years, Kao faced several logistical challenges rooted in its reliance on a network of third-party logistics (3PL) providers and fragmented warehousing systems. These third-party-run warehouses each had different operational processes, IT infrastructures, and inventory systems. This fragmented setup created inefficiencies, reduced visibility, and made it difficult for Kao to maintain high service levels. Seeking to centralize and optimize its logistics operations, Kao made the bold decision to consolidate its wholesale and salon delivery services into a single Central Distribution Center (CDC) located in Cincinnati, Ohio.
This consolidation initiative involved much more than merely moving goods from one warehouse to another. It was a transformative project that required the physical relocation of thousands of products, the migration and reconfiguration of critical logistics and inventory data within Kao’s SAP system, and the coordination of numerous business and IT functions. Kao knew that executing such a large-scale transition without disrupting ongoing operations would require expert support. To that end, the company partnered with management and technology consultancy BearingPoint to lead the planning and execution of this strategic transformation.
Executing a Seamless Transition: Data, Process, and Logistics Alignment
The first phase of the project focused on the foundational task of creating and configuring a new SAP warehouse management system that would support the consolidated operations. This involved the setup of over 10,000 individual storage bins, reclassification and extension of more than 1,500 material master records to align with new product codes, and the modification of storage types and logistics tables to reflect the new warehouse structure.
BearingPoint took a “lift and shift” approach to SAP configuration, ensuring that core data structures and business logic from the legacy systems were transferred directly into the new system architecture while simultaneously customizing the solution to accommodate the additional requirements of the Cincinnati distribution center. This included updating end-to-end logistics processes ranging from sales and order entry to shipment tracking and from inbound purchase receipt to final storage placement.
One of the most technically complex elements was the identification and creation of over 500 unique delivery routes, which had to be incorporated into the SAP system. Each route required careful mapping, scheduling, and integration with SAP’s delivery, transportation, and planning modules. Furthermore, new SAP codes were developed to ensure compatibility across a wide range of essential tools and workflows, including barcode scanners, label printers, shipping documentation, and reporting forms.
Mitigating Risk Through a Phased Rollout Strategy
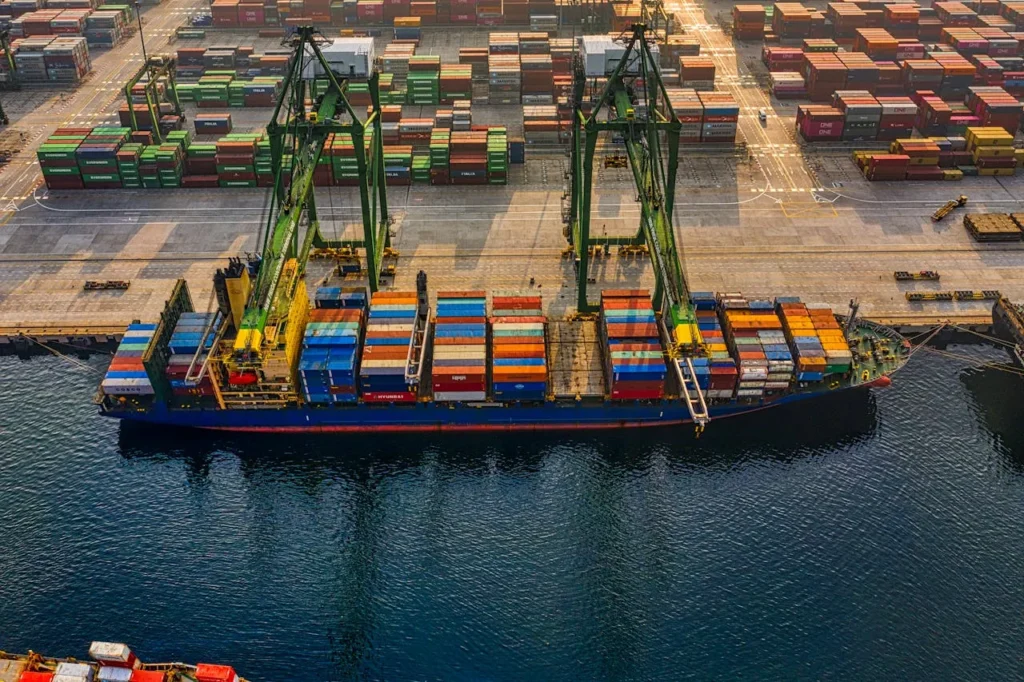
A key component of the project’s success was its phased go-live strategy, designed to minimize risks and ensure continuity of operations. Rather than attempting a full-scale switch all at once, Kao and BearingPoint chose a gradual implementation that allowed the new system to be rolled out in controlled stages.
The phased launch began with the setup and testing of basic purchasing functions, followed by receiving processes and product put-away operations. This was critical for stabilizing the foundation of the warehouse management system before moving to more complex outbound logistics functions. Once the inbound side was stable, high-volume customers were selected for initial pick, pack, and ship services to validate system performance under load and ensure customer satisfaction. Only after successful validation were all remaining customers onboarded.
To ensure seamless continuity and avoid any disruption in customer deliveries during the transition, Kao operated both the existing warehouse and the new CDC in parallel for approximately eight weeks. This dual-warehouse setup allowed logistics teams to compare performance, adjust processes in real time, and validate that the new configuration met all business needs. The transition also served as a live training ground for the logistics staff, who were onboarded to the new processes with the support of BearingPoint’s training and documentation teams.
Driving Results Through Collaboration and Technology Excellence
“The success of this project is a testament to what can be achieved through close collaboration and mutual trust,” said Andreas Fitz, Partner at BearingPoint. “Our work with Kao exemplifies how a well-aligned partnership, grounded in shared goals and a commitment to excellence, can lead to significant operational improvements. From the outset, Kao was clear in its vision and open to innovation, which allowed us to work together seamlessly. The result was a precise, timely, and high-impact transformation of their logistics operations.”
The project also stood out for its emphasis on communication, transparency, and stakeholder involvement. Regular steering committee meetings, real-time performance dashboards, and open lines of communication between IT, business, and third-party vendors created a culture of shared ownership and rapid problem-solving. From warehouse managers to IT administrators, every team had visibility into the transformation journey, allowing for more agile decision-making and faster time to resolution for potential issues.
Achieving Operational Efficiency and Long-Term Competitive Advantage
With the new Central Distribution Center in full operation, Kao has successfully brought its previously outsourced logistics operations in-house, achieving a number of strategic and operational benefits. The move has enabled significant cost savings by eliminating redundant third-party logistics contracts and optimizing transportation routes. More importantly, the centralized approach provides Kao with full visibility across its inventory, warehousing, and distribution functions.
Consolidating logistics data into a single SAP system has allowed the company to gain more accurate forecasting capabilities, better expense management, and improved inventory planning. These enhancements have led to faster delivery times, more reliable service levels, and greater flexibility in responding to market demands. The end-to-end visibility also helps Kao make data-driven decisions that enhance customer satisfaction and align logistics performance with overall business goals.
“Working with BearingPoint was a fantastic experience,” said Christoph Schorn, Associate Director of Logistics at Kao USA Inc. “They didn’t just bring top-tier technical knowledge—they embedded themselves into our team and worked shoulder-to-shoulder with us every step of the way. Their commitment to our success was evident from day one. They delivered the project on time, within budget, and with outstanding results. Their collaborative culture and customer-first mindset made them an ideal partner.”
Positioning for Growth in a Competitive Market
Kao’s successful logistics transformation in the Americas underscores the importance of agile, technology-driven supply chain strategies in today’s dynamic FMCG environment. By consolidating operations, optimizing SAP systems, and investing in high-performing partnerships, the company has laid a strong foundation for future scalability and growth.
With improved logistics efficiency, deeper data insights, and a centralized distribution strategy in place, Kao is now well-positioned to meet rising customer expectations, adapt to evolving market trends, and maintain a competitive edge in the years ahead.