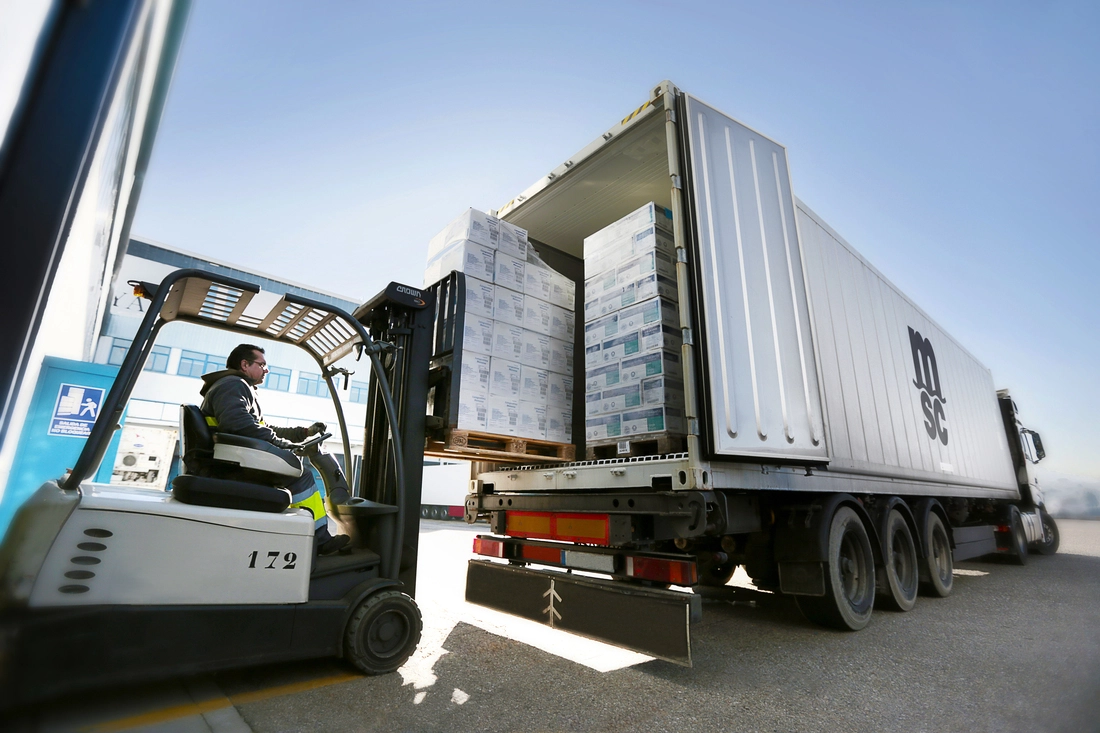
Traditional supply chains are fraught with challenges, but for cold chain operators, the obstacles are even more pronounced. Cold chain management deals with goods that are both time and temperature-sensitive, making it crucial to ensure that products maintain their integrity, safety, and quality throughout the entire supply chain. In this demanding environment, speed, efficiency, and accuracy are paramount, requiring state-of-the-art systems and technologies that can address the unique needs of temperature-controlled logistics.
RealCold, a leading cold chain service provider, has chosen to leverage innovative technology to transform its warehouse operations. The company will deploy Blue Yonder’s Warehouse Management System (WMS) to address the diverse needs of its customers and the growing demands of the cold chain industry. This transition to a digital-first approach will be implemented with the expertise of Netlogistik, a trusted Blue Yonder partner.
RealCold’s Vision and Growth
Founded in 2022, RealCold emerged to meet the evolving demands of the food processing, retail, and foodservice industries. As consumer preferences shift and operational demands grow, RealCold has built a robust network of high-throughput facilities designed to manage temperature-sensitive goods with precision. This network now spans five facilities in key U.S. markets, and with plans to expand further, RealCold is positioning itself as one of the country’s premier domestic cold chain providers.
The company is focused on growth, with two additional cold storage facilities scheduled to open in Florida and Texas in early 2025, followed by another location in New Jersey in Q1 2026. This aggressive expansion reflects the increasing demand for efficient cold chain services in an industry that is both critical and complex.
However, as the company grows, so do the challenges. Managing the logistics of temperature-sensitive goods requires systems that can handle not just the temperature but also the timing, storage, and real-time data monitoring to ensure product integrity at every stage. To continue providing superior service while scaling up operations, RealCold needed a solution that would seamlessly integrate with its existing technology infrastructure and improve the efficiency of its warehouse management processes.
The Need for a Scalable Warehouse Management Solution
As RealCold looked to scale, the company sought a proven, flexible, and resilient Software as a Service (SaaS) solution that could accommodate the unique and evolving needs of the cold chain industry. With its growing national footprint and complex operational requirements across multiple sectors, RealCold needed a system capable of handling high volumes of inventory while ensuring the quality of temperature-sensitive products.
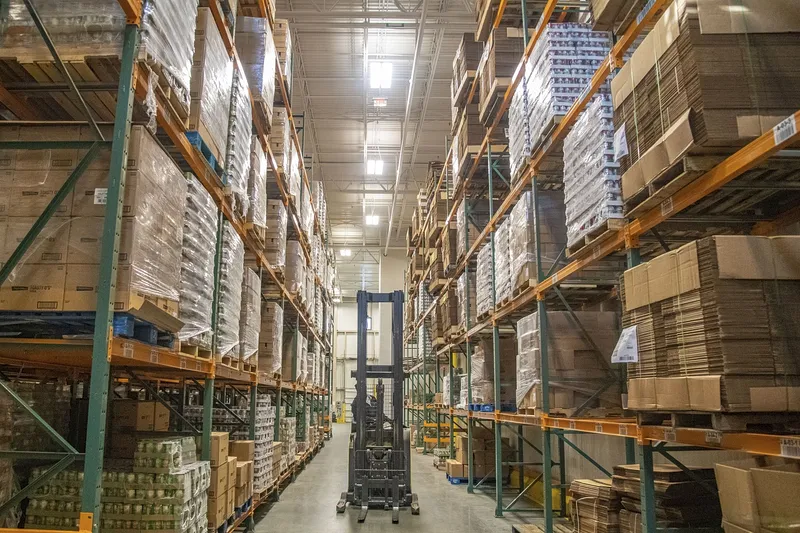
After careful consideration, RealCold selected Blue Yonder’s Warehouse Management System for its advanced capabilities, cold chain experience, and robust software solutions that can handle the intricacies of temperature-controlled logistics. Blue Yonder’s WMS offers an end-to-end solution that not only provides operational efficiency but also the scalability and flexibility required to meet future growth.
The partnership with Netlogistik, an expert in 3PL (third-party logistics) and Blue Yonder implementations, ensures that RealCold can optimize their warehouse operations from day one. Netlogistik brings a wealth of experience to the table, particularly in helping logistics companies scale their operations while keeping costs in check and maintaining high service standards.
Benefits of Implementing Blue Yonder’s Warehouse Management Solution
With Blue Yonder’s WMS, RealCold stands to benefit from several key improvements in its operations, which will ultimately help the company maintain its competitive edge in the cold chain industry.
1. Accelerated Onboarding and System Integration
RealCold’s rapid growth means that onboarding new customers and setting up new warehouse operations quickly is essential. Blue Yonder’s solution will streamline the onboarding process, enabling faster start-up times for new customer operations. The WMS integrates seamlessly with existing systems and technologies, reducing the time it takes to bring new warehouses online and start managing inventory.
This faster implementation also extends to integrating new customer requirements into RealCold’s systems, which will ensure that the company can meet diverse needs right from the start. Whether it’s high-volume case picking, direct-to-consumer deliveries, or customized storage solutions, RealCold will be able to respond quickly and efficiently.
2. End-to-End Visibility and Improved Accuracy
RealCold can now gain comprehensive visibility into all aspects of its warehouse operations with Blue Yonder’s advanced data analytics and monitoring capabilities. This visibility enhances accuracy by reducing errors in inventory management and order fulfillment. With real-time tracking, the company can make better-informed decisions, streamline workflows, and prevent issues that could affect product quality or delivery timeliness.
Whether it’s tracking a shipment through the supply chain or monitoring storage conditions in a temperature-controlled environment, Blue Yonder’s system offers deep insights that help ensure that products maintain their safety and quality standards. This enhanced accuracy directly improves customer service levels, helping RealCold maintain its reputation as a leader in the cold chain space.
3. Intelligent Data Insights for Performance Improvement
By leveraging Blue Yonder’s powerful data analytics tools, RealCold can gain intelligent insights into its operations. The system can process vast amounts of data, uncovering trends and patterns that help optimize warehouse operations, enhance productivity, and drive performance. These insights allow RealCold to continuously refine and improve its processes, ensuring that the company stays ahead of the competition and meets the growing demands of its customers.
With data-driven decision-making, RealCold will also be able to forecast demand more accurately, reduce waste, and optimize storage space. The system’s analytics will ensure that the company can adapt to fluctuations in demand and manage supply chain disruptions effectively, all while maintaining the high standards that customers expect.
4. Customizable and Scalable Workflows
The cold chain industry is highly dynamic, with customer needs constantly evolving. RealCold’s ability to adapt quickly to these changes is crucial to maintaining its market position. Blue Yonder’s WMS offers extensive configuration settings that allow the company to tailor workflows to specific operational requirements. This flexibility means that RealCold can support a wide range of customer needs, from storing perishable goods to handling complex fulfillment processes for different segments, including food processors, retailers, and food service providers.
As RealCold continues to expand and diversify, the scalability of Blue Yonder’s solution will enable the company to grow without sacrificing operational efficiency or customer satisfaction. The system’s flexibility ensures that RealCold can respond to evolving business requirements with ease.
RealCold’s Commitment to Customer Success
RealCold’s CEO, Keith Goldsmith, emphasized the company’s commitment to meeting the diverse storage, distribution, and fulfillment needs of its customers. “Our customers have a wide range of storage, distribution and fulfillment requirements, from high-volume case pick to direct-to-consumer delivery,” Goldsmith explained. “Blue Yonder’s end-to-end warehouse management solution enables us to effectively manage diverse operations while seamlessly integrating with our existing technology and infrastructure, ensuring our clients receive the best possible service and outcomes.”
This customer-centric approach is a key component of RealCold’s growth strategy. By embracing cutting-edge technology and streamlining operations, RealCold aims to offer superior service and continue driving profitable growth in a competitive market.
A Strong Partnership for the Future
Netlogistik’s managing partner, Jagan Reddy, expressed excitement about supporting RealCold’s growth journey. “With our extensive experience in 3PL and Blue Yonder implementations, Netlogistik is excited to support RealCold in scaling their operations to meet dynamic cold chain demands,” Reddy said.
Blue Yonder’s Nafe Hagen also highlighted the potential for RealCold to benefit from the flexibility and scalability of the warehouse management system. “Blue Yonder Warehouse Management offers RealCold the flexibility to rapidly scale and adapt their operations to meet constantly changing demands,” Hagen remarked. “We’re excited to team up with Netlogistik to help RealCold achieve profitable growth and provide their customers with a competitive advantage.”
With the powerful combination of Blue Yonder’s technology, Netlogistik’s expertise, and RealCold’s commitment to customer success, the company is well-positioned to continue leading the cold chain industry into the future. As demand for temperature-sensitive logistics grows, RealCold’s innovative approach will ensure that it remains at the forefront of the sector.
Read more: Cold Chain Operations Boosted: RealCold Partners with Blue Yonder to Optimize Warehouse Efficiency