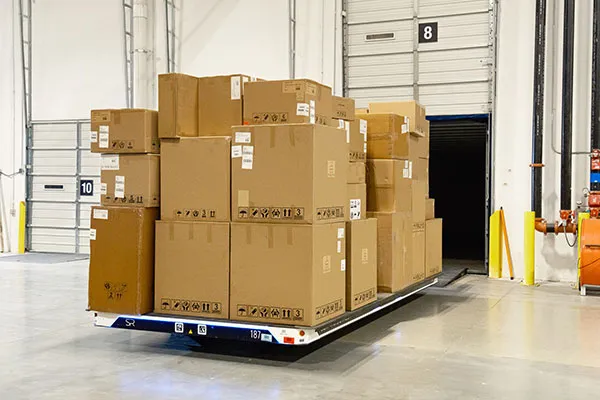
Four Hands Transforms Warehouse Operations with Slip Robotics, Achieving Unprecedented Efficiency Gains
Revolutionizing Logistics with Automation
In a rapidly evolving logistics landscape, efficiency, speed, and precision are crucial for businesses striving to meet increasing customer demands. Four Hands, a global leader in lifestyle home furnishings design and distribution, has embraced this shift by integrating Slip Robotics’ innovative SlipBot technology into its warehouse operations. This partnership has yielded remarkable results, optimizing loading and unloading processes, reducing manual labor, and enhancing safety measures.
The Growing Need for Automation in Warehousing
The home furnishing industry has faced significant logistical challenges in recent years. With a diverse product mix that includes items ranging from lightweight decorative accessories to heavy furniture pieces, handling inventory efficiently has become increasingly complex. As e-commerce continues to drive higher consumer expectations for fast delivery, companies like Four Hands must innovate to keep pace. Traditional warehouse operations, relying heavily on manual labor, often struggle with bottlenecks that impede throughput and delay shipments.
By adopting Slip Robotics’ cutting-edge automation solutions, Four Hands has positioned itself at the forefront of warehouse innovation. The integration of SlipBots has led to a fourfold increase in throughput, a 75% reduction in trailer unloading time, a 50% reduction in loading time, and a 50% decrease in product touches—a game-changing transformation for the company’s logistics network.
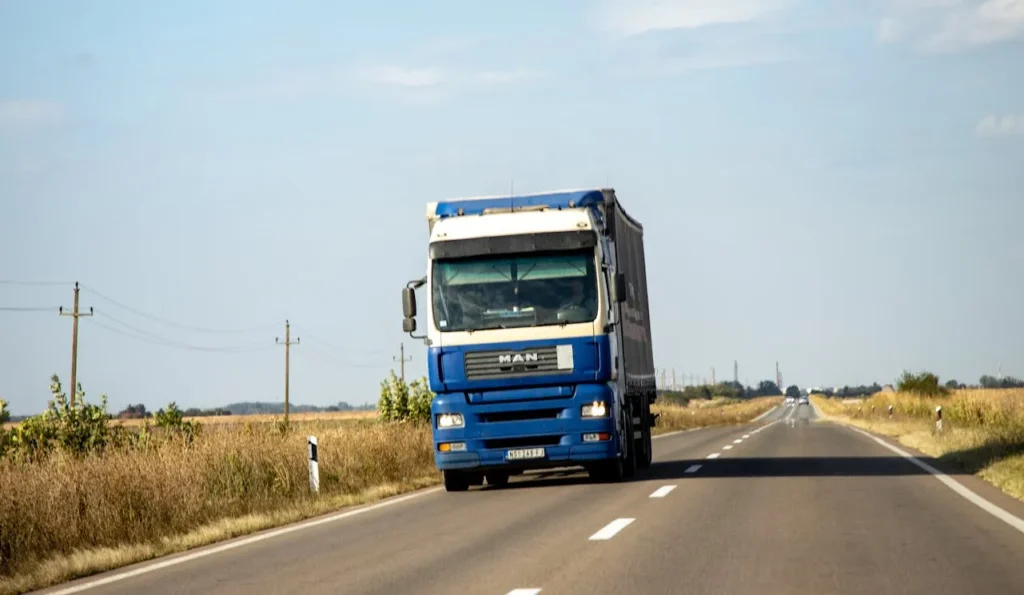
Addressing Key Warehousing Challenges
Prior to deploying SlipBots, Four Hands faced significant inefficiencies in its trailer loading and unloading processes. Each trailer required a team of 8–10 workers, often taking up to 90 minutes to fully load or unload a single shipment. The physically demanding nature of this work not only led to wear and tear on employees but also increased the risk of errors, delays, and workplace injuries.
The challenge was further compounded by the company’s complex logistics network, which includes multiple warehouse facilities. Transporting heavy furniture pieces between buildings added another layer of inefficiency, making it imperative to find an automated solution that could streamline the entire process.
The Game-Changing Role of SlipBot Technology
Slip Robotics’ autonomous SlipBots were the ideal solution. These automated loading robots are designed to tackle warehouse inefficiencies head-on, offering the following advantages:
- Rapid Deployment: Unlike traditional automation solutions that require significant IT infrastructure changes, SlipBots operate without Wi-Fi or IT integration, making them easy to deploy and scale.
- Multi-Access Loading & Unloading: Traditional loading methods restrict workers to a single access point. SlipBots enable operators to load and unload from multiple sides, drastically improving efficiency.
- Optimized Trailer Space Utilization: By loading SlipBots on the dock rather than directly into trailers, warehouse teams can maximize trailer capacity, reducing the number of trips required for shipments.
- Enhanced Safety & Reduced Physical Strain: With a 50% reduction in manual product touches, employees experience less physical exertion, reducing the risk of workplace injuries and fatigue.
Michael Leuckmeyer, Process Engineer at Four Hands, emphasized the seamless integration of SlipBot technology: “The SlipBots were operational within days, and the local tech support and training exceeded our expectations. The rapid adoption and enthusiasm from our team was remarkable, and the constant support from Slip Robotics sets them apart.”
Driving Efficiency, Safety, and Scalability
The implementation of SlipBots has fundamentally reshaped warehouse operations at Four Hands. By reducing unloading time by nearly 75% and cutting loading times in half, the company has significantly increased overall operational efficiency. These time savings translate directly into faster order fulfillment and improved customer satisfaction.
Moreover, the reduction in manual handling has improved employee safety, as workers no longer need to endure extreme temperatures inside trailers or physically demanding lifting tasks. The efficiency gains also help lower operational costs, allowing Four Hands to reinvest resources into further innovation and business expansion.
Billy Malady, VP of Operations at Four Hands, highlighted the transformative impact: “We’ve reduced unloading time by almost 75%, loading times by 50%, and product touches by 50%. These improvements have allowed us to reimagine how we handle trailers, making our entire supply chain more resilient and adaptable.”
The Future of Warehouse Automation at Four Hands
As Four Hands continues to expand its operations, the company sees Slip Robotics as an integral part of its long-term strategy. With plans for additional warehouse facilities, the ability to scale automation quickly and seamlessly will be critical to maintaining operational excellence.
Jim Anderson, Chief Operating Officer at Four Hands, reaffirmed this commitment: “It really does what it’s advertised to do. Being able to implement solutions that help the human provides a practical and realistic solution that delivers value.”
Looking ahead, Four Hands aims to further leverage automation technologies like SlipBots to optimize supply chain processes, increase agility, and strengthen its competitive edge in the home furnishings industry.
About Four Hands
Based in Austin, Texas, Four Hands is a premier global designer and wholesaler of trendsetting lifestyle home furnishings. The company has earned widespread acclaim for its ability to blend diverse styles, materials, and textures, creating distinctive furniture pieces that resonate with modern consumers. Four Hands has been recognized on the Inc. 5000 List of Fastest Growing Companies 15 times and has received multiple industry accolades for its innovation and business excellence.
About Slip Robotics
Slip Robotics specializes in autonomous loading solutions, helping businesses auto-load and auto-unload any truck in just 5 minutes. Their SlipBot Automated Loading Robots (ALRs) require no Wi-Fi or IT integration and can be deployed at any dock, in any trailer, delivering 10x improvements in safety, speed, and cost savings. Fortune 500 companies, including John Deere, GE Appliances, Nissan, and Valeo, rely on Slip Robotics to revolutionize their supply chain operations.