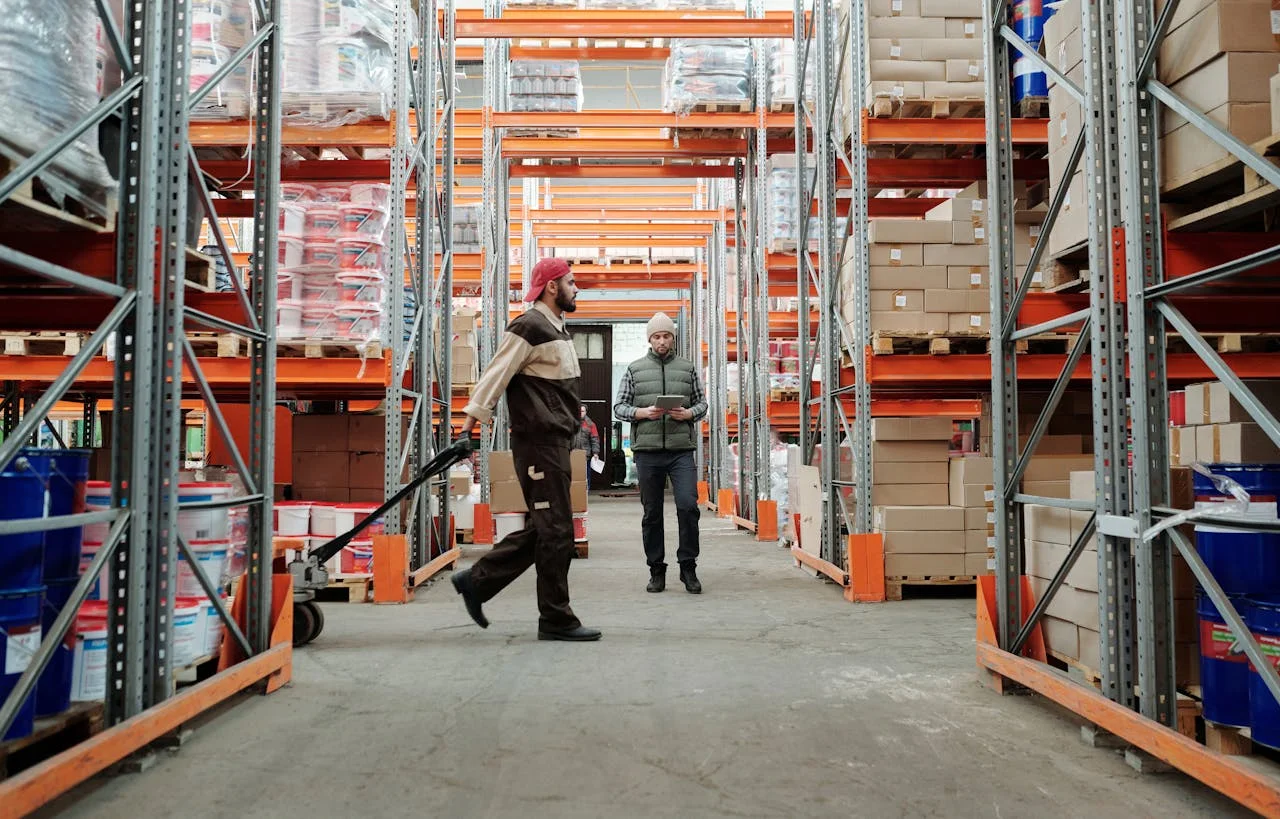
Impinj, Inc. (NASDAQ: PI), a leader in RAIN RFID technology and the Internet of Things (IoT), has unveiled the findings of its Supply Chain Integrity Outlook 2025 report. The report, based on a survey of 1,000 supply chain managers in the U.S., exposes a significant gap in data accuracy, leaving many organizations struggling to achieve the visibility, insights, and reliability required for confident supply chain management. While 91% of supply chain managers believe they have the tools to ensure accurate visibility, only 33% consistently obtain real-time, accurate inventory data.
This gap in data accuracy creates challenges for supply chain leaders, particularly in addressing issues such as counterfeit goods, shrinkage, theft, misloads, delivery errors, sustainability goals, and the integration of AI into supply chain operations. Additionally, over half (52%) of supply chain managers report difficulties in responding to sharp spikes in customer demand driven by trends on social media and influencer-driven movements. Nearly half (47%) also cite fluctuations in demand from the rise of social media storefronts (49%) and the growing popularity of the thrift movement (47%) as key challenges.
Priorities for Supply Chain Managers
The report highlights the most pressing supply chain integrity issues, with several sectors placing particular emphasis on the following priorities:
Counterfeit Goods in Retail: A significant 65% of supply chain managers in retail acknowledge the challenge of reducing counterfeit goods in the supply chain. Nearly all (98%) retail supply managers are actively working to combat counterfeiting, with key strategies including the adoption of authentication technologies (44%) for goods in transit, general goods verification (42%), and increased authentication checkpoints throughout the supply chain (40%).
Shrinkage and Theft in Retail: About 60% of retail supply chain managers face challenges in reducing shrink and theft, with 99% investing in solutions to address these issues. The primary measures being implemented include increased security checkpoints during transit and delivery (48%) and the adoption of new tracking technologies (41%).
Shrinkage in the Food, Grocery, and Restaurant Sector: Shrinkage is a particularly pressing issue for supply chain managers in the food, grocery, and restaurant sectors, where 82% report challenges in minimizing shrink. The primary causes of shrink are shoplifting (45%), food spoilage (37%), and food waste (35%). To tackle these, organizations are investing in new technologies for surveillance (45%), goods tracking (44%), and waste reduction (44%).
Misloads and Delivery Errors in Transportation and Logistics: In the transportation and logistics sector, nearly 74% of managers express concern over the increasing frequency of misloads, delivery errors, and load planning issues (LPPs). The most common errors are linked to last-mile misloads (24%) and label inaccuracies (22%). To address these, 48% of transportation and logistics firms plan to invest in enhancing shipment accuracy and reducing delivery errors as part of their broader sustainability initiatives.
Overall, the report underscores the critical role of accurate, real-time data and technology adoption in overcoming key challenges facing supply chain managers and meeting the evolving demands of today’s market.